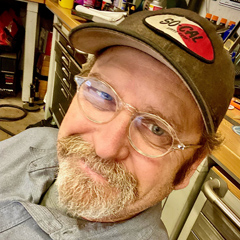
How to Use a Bead Roller
Mark SimpsonWhen fabricating sheet metal parts, using a bead roller can add strength to the panels and return new parts to a factory look. Join Mark Simpson in this introduction to bead rolling as he demonstrates how to use a bead roller to roll flanges and beads.
If you're really serious about doing metal fabrication, one of those tools that is really a good plus to have in your shop is a bead roller. Bead rollers are available at a wide range of price range. You can get them at Harbor freight for a couple hundred bucks or more professional models up to a couple thousand dollars even. For me I use it for a lot of things in the shop where I need to fabricate panels to look like existing panels or to strengthen large pieces of steel where you might get a pop canning and you wanna run a couple of beads across it just to add some strength without adding any weight to it. And one of the things, even on our Project 57 here when I replaced the entire trunk floor I used the bead roller to actually go in and recreate the factory beads and roles in the floor itself, that way it had the look of the original yet it still had all the strength of actually having those contours put into the steel.
With that, lets look at a few of the different beads you can make. The most common one are beads, are temple beads and flanges. A flange would be created when you roll metal through and it just kind of steps the edge, and that way you can attach it to another piece of metal and it would come up flush. This gives you a nice strong lap joint without much effort. The another thing that we've create is called beads.
Here's a test sample I ran. We ran through here where we've created different sized beads and then kept them off. And I'll show you how we do that as well. And that's one of the things we had to do on the floor, on the trunk floor of this 57, was to create a number of these next to each other so we had some built in strength spots in the floor. Another thing you can use it for is tipping edges.
Sometimes you have an irregular shape and you wanna bend the edge up to either weld to another surface or to create a flange around it. This can be really difficult with a box break, box and pan break, because that wants to essentially break a straight edge, whereby tipping, we're allowed to actually create a tip in the metal that of an irregular shape. So let's take a look at some of these. First we'll make a simple flange on a piece of metal. This is the bead roller itself.
It consists of a frame, and then this frame has a throat. This throat here determines you know, the size of material that can actually be bead rolled in the machine. In this case, it's a 24 inch throat which essentially allows us to roll the center of a 48 inch piece wide piece of metal. Next we have the motor. The motor is, this one's got an electric motor, some will have a hand wheel back here, just a less expensive way to create it, and some guys actually prefer it because they can kinda just feed it along as they go and they have a better feel for it.
Up on top we have this crank. The crank is used to apply tension to between the two dies. The more tension of course, the more you'll form the metal. Too much tension of course you'll start to stretch the metal too. And then of course the two dies.
The dies determine what the tool will do. In this case we have it set up with flanging dies, and what this will do is they'll create a step in the edge of the metal. And to do that, we simply take a piece of metal, feed it into the rollers and follow the edge. If we need more attention or if we need a bigger draw, sometimes you need to make a couple of passes or two or three passes to get the depth that you want. In this case, we'll make three passes, and that creates a step in this metal.
Now I can bring that up against another piece of metal and suddenly I've got a seamless finished between two pieces of metal that I can weld on and I still have a lot of structure on that seam. Next I'm gonna show you how to set up the dies. Right now like I said, we've got the flanging dies in there. And it's just a couple of Allen screws. Kurt take the tension off of everything.
And there are literally for any good bead roller, there are literally hundreds of dies that are available to create a wealth of different things. In this case, next we're gonna try making a bead. And a bead is simply a raised portion. Well, there's a couple of different kinds of beads. One is a bead that extends off the metal and the other is a bead contained within the metal, in a lot of cases you got to finish that off, and we'll show you how to do that.
We're going to put in a guide stop. Guide stop basically ensures that as I pass the metal through that it remains straight and true. This will give us a surface to actually run the metal up against, so when we're creating the bead, it will be in a consistent place each time we make a pass through there. And there you have a bead that actually extends off the edge of the panel. And next we'll show you how to make a bead that stays within the panel and how to finish the ends off.
This will give us a reference point where to start and stop each time. Okay. Now you can see how this bead, you know, it finished off to here but we need to close off the ends. In order to do that, we use a tool. Actually most of these are made by the fabricators themselves.
I haven't found a good source for these yet, but it's just like a half round piece of pipe, easy enough to make for most guys. And it's just a matter of coming in and And if you look closely, you'll see that this kind, because we're shrinking, basically because this metal is puckering up and shrinking, this part of the panel, the panel itself will want to flex and contour out. And that's just a matter of going in and restretching out your panel in the places, around that. So, essentially that's how you close off the end of a bead. And that's, in this is a bead that extends off the edge of the material itself.
could please take more about the metal material and beads materials made of?