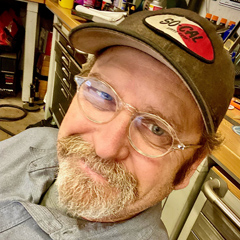
Shaping Aluminum Alloy Sheet
Mark SimpsonThe history of shaping aluminum sheet metal for use on classic automotive bodies is a fascinating journey that involves technological advancements, skilled craftsmanship, and the pursuit of lightweight and aerodynamic designs. Aluminum was first used in the early 20th century for automotive bodies due to its lightweight properties and corrosion resistance. It provided an alternative to traditional steel, which was heavier and more susceptible to rust. However, the use of aluminum was limited primarily to luxury and high-end vehicles due to its higher cost and the complexity of working with the material.
In the early days of automotive manufacturing, aluminum sheet metal was shaped using hand-forming techniques. Skilled metalworkers, known as panel beaters or coach builders, used hammers, mallets, and various shaping tools to form the metal sheets into desired contours and curves. This process was labor-intensive and required a high level of craftsmanship, but it allowed for intricate and custom designs. As automotive production expanded and demand increased, the need for more efficient and cost-effective shaping methods arose. This led to the development of automotive presses that could stamp and form aluminum sheets into predefined shapes. These presses used dies and hydraulic systems to apply pressure and shape the metal, significantly reducing production time and costs.
Classic automotive manufacturers and designers embraced aluminum for various reasons. Apart from its lightweight nature and corrosion resistance, aluminum offered better heat dissipation, which was essential for performance and racing cars. The metal’s malleability allowed for unique and aerodynamic designs, enhancing the aesthetics and performance of classic vehicles.
However, working with aluminum presented challenges as it was prone to cracking and required specialized welding techniques. However, advancements in welding technologies, such as TIG (Tungsten Inert Gas) welding, made it possible to join aluminum sheets without compromising their integrity. Additionally, aluminum alloys were developed to improve strength and durability while maintaining the material’s favorable properties.
Today, classic automotive restorations often involve traditional hand-forming techniques. Despite advancements in technology, hand-crafted aluminum bodywork remains an art and a revered skill. Many classic car enthusiasts and collectors value the authenticity and craftsmanship of hand-shaped aluminum bodies, which carry a sense of heritage and tradition.
Shaping aluminum sheet metal for use on classic automotive bodies involves a series of steps that require skill, and the right tools. To guide us through the process we joined up with master craftsman Bruce Macleod of the Contour Academy Workshop. Bruce explains, the correct hand tools you’ll need and how hammer forms & jigs are used to help define the final shape.
After defining the rough shape of the panel it must be annealed before shaping the aluminum. Annealing softens the Aluminum sheet metal and prevents the metal from hardening and cracking while being shaped. For this demonstration only readily available and affordable hand tools are used to create the double contour shape in the panel. While the processes of shaping aluminum sheet metal panels are relatively straightforward, like any skill you’ll only become proficient in them with practice.