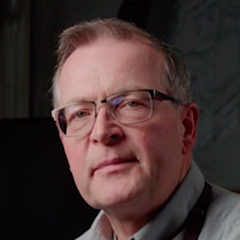
TIG Fusion Butt Welding
Bruce MacleodTungsten Inert Gas (TIG) welding, also known as Gas Tungsten Arc Welding (GTAW), is a welding process commonly used in automotive fabrication. It involves the use of a non-consumable tungsten electrode to produce the weld and an inert gas, typically argon, to protect the weld area from atmospheric contamination.
The history of TIG welding dates back to the early 20th century when it was developed for joining non-ferrous metals such as magnesium and aluminum. The process was first patented in 1941 by Russell Meredith, who called it “Heliarc” welding. However, it was during World War II that TIG welding gained significant attention and application due to its versatility and ability to produce high-quality welds.
In the automotive industry, TIG welding found widespread use in the fabrication of various components and structures. It became particularly important for welding aluminum, which is commonly used in the construction of car bodies, engine components, and other parts due to its lightweight and corrosion-resistant properties.
TIG welding offers several advantages in automotive fabrication. Firstly, it allows for precise control over the welding process, making it suitable for intricate and critical welds. The non-consumable tungsten electrode remains constant throughout the welding process, providing a stable arc and better control over the heat input.
Secondly, TIG welding produces high-quality welds with excellent aesthetics. The use of an inert gas shield prevents the weld area from oxidizing or reacting with the surrounding atmosphere, resulting in clean, visually appealing welds.
Thirdly, TIG welding is versatile and can be used to weld a wide range of metals, including aluminum, stainless steel, titanium, and copper alloys. This versatility makes it a preferred choice in automotive fabrication, where different metals and alloys are often used.
In this video we join up with Bruce Macleod of the Contour Autocraft Academy, who demonstrates how to fusion butt weld two steel panels together, in a manner similar to how patch panels are welded into exterior body panels. By “fusion TIG butt welding” no fill rod is added, reducing time spent grinding and ensuring the seam is made from the same material as the base metal. Macleod takes you step-by-step through safety, setup, controls, welding and finishing a panel to seamless perfection. If you’re serious about welding and fabrication this is one of those “Must-Have” skills you need to know.
Premium Membership
Unlock exclusive member content from our industry experts.
- 24/7 Access to Premium Videos, Tips, and Techniques
- Step-by-Step Instructional Demos, Guides, and Tutorials
- 50% Off Video Downloads Purchased in the Classic Car Restoration Shop
- Access to Ask the Expert Program
Unlock exclusive member content from our industry experts.
- 24/7 Access to Premium Videos, Tips, and Techniques
- Step-by-Step Instructional Demos, Guides, and Tutorials
- 2 Full-Length Video Downloads to Watch Offline
- 50% Off Video Downloads Purchased in the Classic Car Restoration Shop
- Access to Ask the Expert Program
Gold Membership
$304 Value
Get everything included in Premium plus exclusive Gold Membership benefits.
- 24/7 Access to Premium Videos, Tips, and Techniques
- Step-by-Step Instructional Demos, Guides, and Tutorials
- 10 Full-Length Video Downloads, added to your account, to Watch Offline
- ‘Wheel Bolt Circle’ Downloadable Guide, added to your account
- Discounts on Purchase-to-Own Content in the Classic Car Restoration Club Shop
- Access to Ask the Expert Program