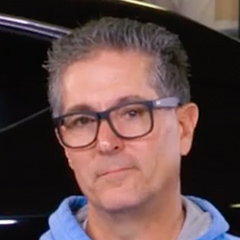
Selecting the Right Air Hoses & Fittings
Terry WrightIn the early days of automobile painting, cars were painted by brush, then hand-rubbed into a smooth finish. But as assembly lines began, the need to paint cars quickly and efficiently became a driving factor to the introduction of spray painting. Cars are still spray painted today, although in most cases the assembly line painter has been replaced by a robotic painting system. This allows manufacturers to have fast and repeatable results without the possibility of human error.
Even the best spray painting equipment in the world will deliver poor results without a good air supply. Most starting hobby painters concern themselves first with air volume at the compressor and overlook the many considerations in building a system that works well for both equipment and painting.
We met up with automotive paint professional Terry Wright to discuss what steps every painter should take to achieve better results. Wright admits air volume is a big concern; it’s air volume “at the gun” that should be the objective. As the spray gun term “HVLP” (High Volume Low Pressure) implies, the importance of getting a lot of volume to the gun is key to success.
Terry points out the most common bottleneck in home shops is the selection of hose fittings. Common type “M” fittings work well for smaller shop tools, but they lack the volume needed for modern spray equipment. High-Flow fitting will eliminate the bottleneck and make both your spray equipment and your shop tools perform better.
He also points out that the air hose itself can be a point of restriction, and emphasizes the importance of keeping the hose length as short as possible to prevent pressure (“line-drop”). 3/8-inch hoses and fittings are strongly recommended, including making certain the air hoses have 3/8-inch ends on them. Wright also shares some great tips on setting up your system for the most efficiency.
Having air pressure adjustability at the gun is important, but selecting the right type of regulator is key as well. A diaphragm-type regulator will give you consistent pressure without restricting flow. He points out there are workarounds to adjusting pressure depending on the shop setup.
Terry points out the need to have a good dry-air supply will ensure good results. He also shares the importance of taking the time to consider ALL of the components in your air system and making the right choices to ensure they’ll all work well together.
Premium Membership
Unlock exclusive member content from our industry experts.
- 24/7 Access to Premium Videos, Tips, and Techniques
- Step-by-Step Instructional Demos, Guides, and Tutorials
- 50% Off Video Downloads Purchased in the Classic Car Restoration Shop
- Access to Ask the Expert Program
Unlock exclusive member content from our industry experts.
- 24/7 Access to Premium Videos, Tips, and Techniques
- Step-by-Step Instructional Demos, Guides, and Tutorials
- 2 Full-Length Video Downloads to Watch Offline
- 50% Off Video Downloads Purchased in the Classic Car Restoration Shop
- Access to Ask the Expert Program
Gold Membership
$304 Value
Get everything included in Premium plus exclusive Gold Membership benefits.
- 24/7 Access to Premium Videos, Tips, and Techniques
- Step-by-Step Instructional Demos, Guides, and Tutorials
- 10 Full-Length Video Downloads, added to your account, to Watch Offline
- ‘Wheel Bolt Circle’ Downloadable Guide, added to your account
- Discounts on Purchase-to-Own Content in the Classic Car Restoration Club Shop
- Access to Ask the Expert Program